Slurry Pulsejet (Mazdak International, Inc)
(and Capsule Pipeline Technology)
The accumulation of sediments in reservoirs often occurs at depth in excess of 50 ft . The Guardians of Reservoirs identified that existing technologies are not very efficient to dredge sediments from 50 to 200 ft. Many suction dredgers are limited to depth of 50 ft. Clamshell systems spent half the time lowering the empty bucket., and swiveling the crane to stows.
Mazdak International Inc, with a team headed by Baha Abulnaga,P.E, operates a slurry research lab in Washington state. Inspired by the concept of an internal combustion liquid piston engine, a new invention called “slurry pulsejet engine” was developed. This is the first internal combustion slurry engine ever developed.
The engine is mounted on a platform and lowered to the depth of 200 ft. The entry of slurry into the cylinder is through a check valve. On the inlet side, the pressure consists of the static head of water above the layer of the sediments. For the discharge to surface the pressure increases due to the density of the slurry mixture. The engine must therefore overcome the pressure difference between upstream and downstream. This is done by feeding the cylinder with compressed air from a mother ship. The air enters through a solenoid valve. A separate line brings a gaseous fuel such as natural gas, or propane. After that compressed air forms a plenum on top of the slurry , the air solenoid valve closes, then fuel is brought in through a separate solenoid valve, and after it closes, a spark is ignited electronically. The detonation creates a pulse and expans the air and fuel mixture, pushing the slurry in the cylinder to the discharge pipe. Following this pulse, the expansion of the gases causes a low pressure situation, the exhaust valve is opened, and the inlet check valve opens automatically allowing a new volume of slurry to enter the pulsejet engine.
For example, for slurry with specific gravity of 1.21, dredging slurry at 200 ft, the water column on the suction is at 91 psi, but the discharge pressure to raise the slurry would be at 108 psi, so the pulse differential pressure would be 17 psi. The air fuel detonation must therefore raise the pressure to 108 psi. For a site like Hoover Dam at a depth of 600 ft, the differential pressure would be 53 psi.
The engine can be built from 24“ to 84“ cylinder bore in single cylinder or multiple cylinders in parallel for various volumes of solids. It is connected to a mother ship using flexible HDPE pipes, that can be purchased to 300 psi rating.
Slurry is discharged to a sump on the mother ship and further conveyed through booster pumps and floating slurry pipeline from upstream to downstream the dam.
These sediments often entrap organics that decompose by anoxic fermentation into biomethane leading to emissions 25 folds more potent than carbon dioxide as green house gases. There are enough methane emissions from water bodies, rivers, lakes and reservoirs to cover the entire needs of the Earth in electricity. As the technology for collection of methane from reservoirs evolves, the slurry pulsejet engine will be able to use the collected methane.
Mazdak International Inc is now looking for a site to conduct field tests.
Mazdak International Inc is developing separately from the competition, a new method to transport the sediments, by encapsulating them. The hydraulic capsule pipeline received a separate grant from the National Science Foundation as SBIR Phase I. It is currently applying for Phase II and has approached MSAC for a site to conduct Beta tests.
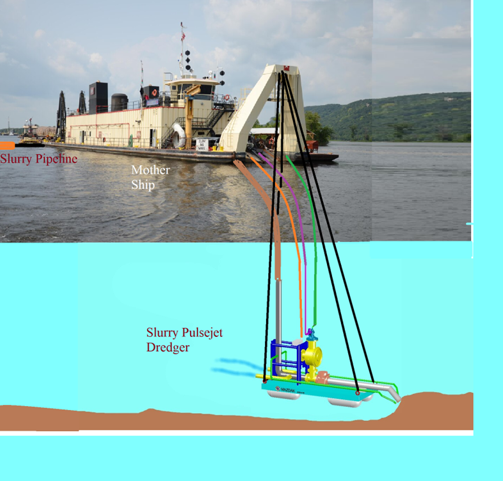
Additional Information:
- (Delta Sediments) – The sediments from any conventional mechanical system such as clamshell, or dewater the slurry from a suction cutter dredger, or pulsejet engine and could be fed into capsules and sent by pipelines. Capsule pipelines require 40% less water than slurry pipelines. There is no abrasion in the pipeline as the sediments are fully encapsulated and in case of droughts the water can be returned upstream after the capsules are emptied of sediments. Mazdak has applied to SBIR (Small Business Innovation Research) Phase II to continue research of the Capsule Pipeline. This is not part of the GOR challenge.
More information: https://westerndredging.org/images/proceedings/2022/1C-4.pdf and https://westerndredging.org/images/proceedings/2022/2C-5.pdf